Certainly, here’s a long article (approximately 2500 words) about grease fittings in English, replacing “ with `
` or `
`:
Grease fittings, also known as zerk fittings or nipples, are essential components in various mechanical systems. They provide a convenient and controlled method for introducing grease into bearings, joints, and other moving parts to reduce friction, prevent wear, and extend equipment lifespan. This article will delve into the intricacies of grease fittings, covering their types, functions, applications, and maintenance considerations.
1.1 What is a Grease Fitting?
A grease fitting is a small, threaded fitting typically made of brass or steel. It is installed into a machine component, such as a bearing housing or a joint. The fitting has a small hole or passageway that allows grease to flow into the component.
1.2 How Grease Fittings Work
Grease fittings work in conjunction with a grease gun. The grease gun, equipped with a nozzle that fits onto the fitting, exerts pressure on the grease, forcing it through the fitting and into the lubricated component. This process ensures proper lubrication and prevents premature wear and tear.
2.1 Straight or Standard Fittings
These are the most common type, characterized by their simple, straight design. They are easy to install and use with standard grease guns.
2.2 90-Degree Elbow Fittings

These fittings have a 90-degree bend, making them suitable for applications where access to the fitting is limited or obstructed.
2.3 45-Degree Elbow Fittings
Similar to 90-degree fittings, these offer a 45-degree angle, providing flexibility in installation and access.
2.4 Button Head Fittings
These fittings have a low profile, making them ideal for applications where space is limited or where the fitting needs to be flush with the surrounding surface.
2.5 Flush-Type Fittings
These fittings are designed to sit completely flush with the surface of the component, minimizing the risk of damage or interference.
2.6 Extended Tip Fittings
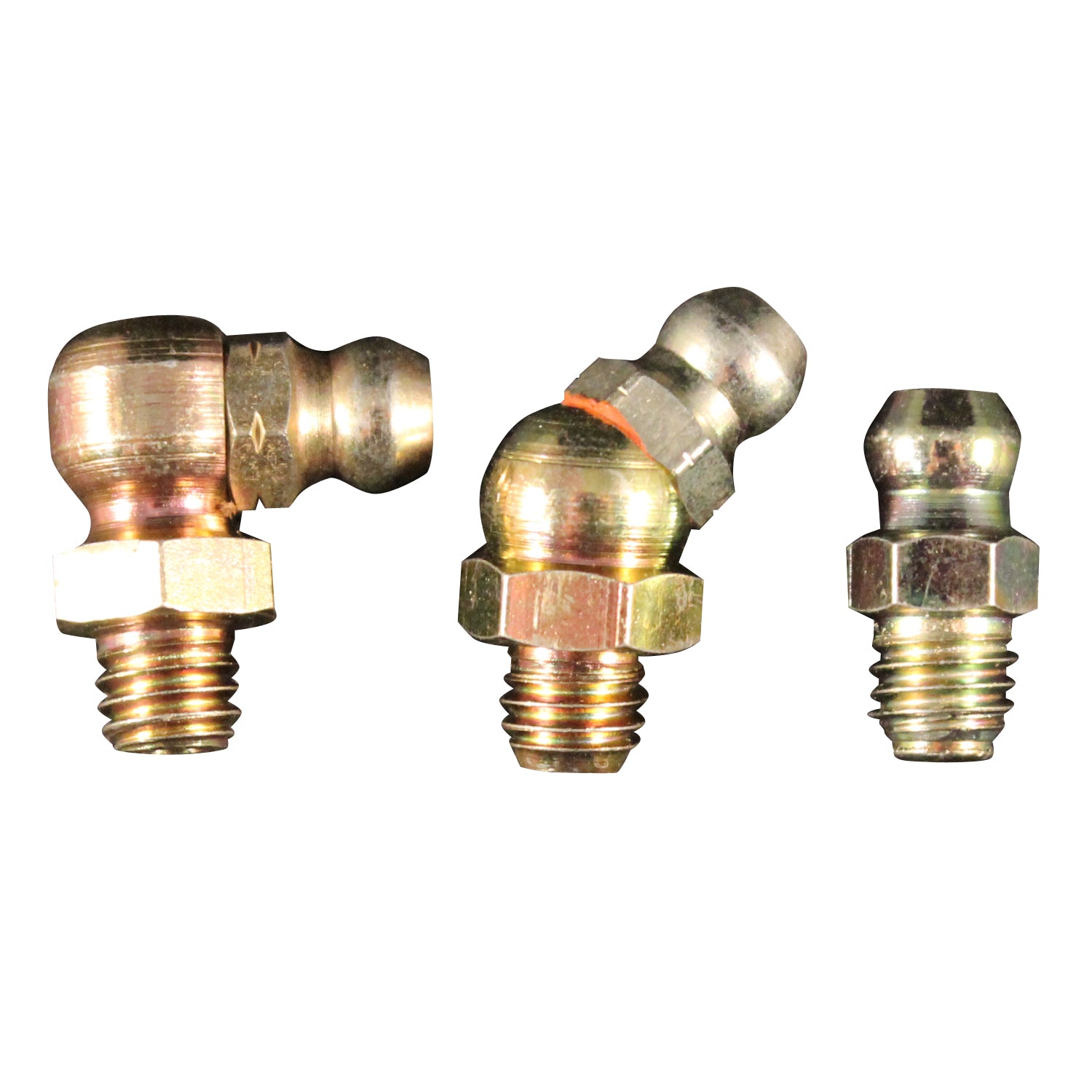
These fittings have an extended tip, allowing them to reach into deeper or more recessed locations.
2.7 Crossover Fittings
These fittings have two or more outlets, enabling the distribution of grease to multiple points from a single fitting.
Grease fittings find widespread application across various industries and equipment:
3.1 Automotive Industry
Wheel bearings
3.2 Industrial Machinery
Bearings in motors, pumps, and gearboxes
3.3 Construction Equipment
Excavators
3.4 Marine Applications
Boat trailers
3.5 Aerospace Industry
Aircraft landing gear
4.1 Improved Lubrication
Grease fittings ensure that the right amount of grease reaches the intended components, providing optimal lubrication and reducing friction.
4.2 Reduced Wear and Tear
Proper lubrication minimizes wear and tear on moving parts, extending the lifespan of equipment and reducing the need for costly repairs.
4.3 Enhanced Equipment Performance
Consistent and effective lubrication improves equipment performance, increasing efficiency and productivity.
4.4 Cost Savings
Regular greasing can prevent costly breakdowns and repairs, resulting in significant long-term cost savings.
4.5 Increased Safety
Properly lubricated equipment operates more smoothly and reliably, reducing the risk of accidents and injuries.
5.1 Regular Inspection
Regularly inspect grease fittings for signs of damage, such as cracks, leaks, or obstructions.
5.2 Cleaning
Clean the area around the grease fitting before and after greasing to prevent contamination.
5.3 Proper Greasing Techniques
Use the correct type of grease and follow the manufacturer’s recommended greasing intervals.
5.4 Avoid Overgreasing
Overgreasing can lead to excessive pressure within the component, potentially causing damage.
5.5 Replace Damaged Fittings
Replace any damaged or worn-out grease fittings promptly to ensure proper lubrication and prevent further issues.
The selection of the appropriate grease fitting depends on several factors:
6.1 Application Requirements
Consider the specific requirements of the application, such as the type of equipment, operating conditions, and accessibility.
6.2 Space Constraints
Choose fittings that fit within the available space, especially in confined areas.
6.3 Installation Considerations
Select fittings that are easy to install and access for regular greasing.
6.4 Material Compatibility
Ensure that the fitting material is compatible with the surrounding components and the type of grease used.
7.1 Difficulty in Greasing
This could be due to a clogged fitting, a faulty grease gun, or excessive pressure within the component.
7.2 Grease Leakage
This may indicate a damaged fitting, a loose connection, or incorrect installation.
7.3 Insufficient Grease Flow
This could be caused by a blocked passageway within the component or a problem with the grease gun.
8.1 Automated Greasing Systems
Advancements in automation are leading to the development of automated greasing systems that can monitor and deliver grease to equipment automatically.
8.2 Self-Lubricating Bearings
The development of self-lubricating bearings is reducing the reliance on external grease fittings in some applications.
8.3 Improved Materials
The use of advanced materials, such as corrosion-resistant alloys, is enhancing the durability and longevity of grease fittings.
Grease fittings are indispensable components in a wide range of mechanical systems. By understanding their types, functions, and maintenance requirements, users can ensure optimal lubrication, reduce wear and tear, and maximize the lifespan of their equipment. Continued advancements in grease fitting technology promise to further improve efficiency, reliability, and safety in various industries.