Certainly, here’s a long article (approximately 2500 words) about grease fittings in English, replacing “ with `
` or `
`:
Grease fittings, seemingly simple components, play a crucial role in the smooth and reliable operation of various mechanical systems. They are essential for the efficient lubrication of moving parts, minimizing wear and tear, and extending the lifespan of machinery. This article provides a comprehensive overview of grease fittings, covering their types, functions, applications, and maintenance considerations.
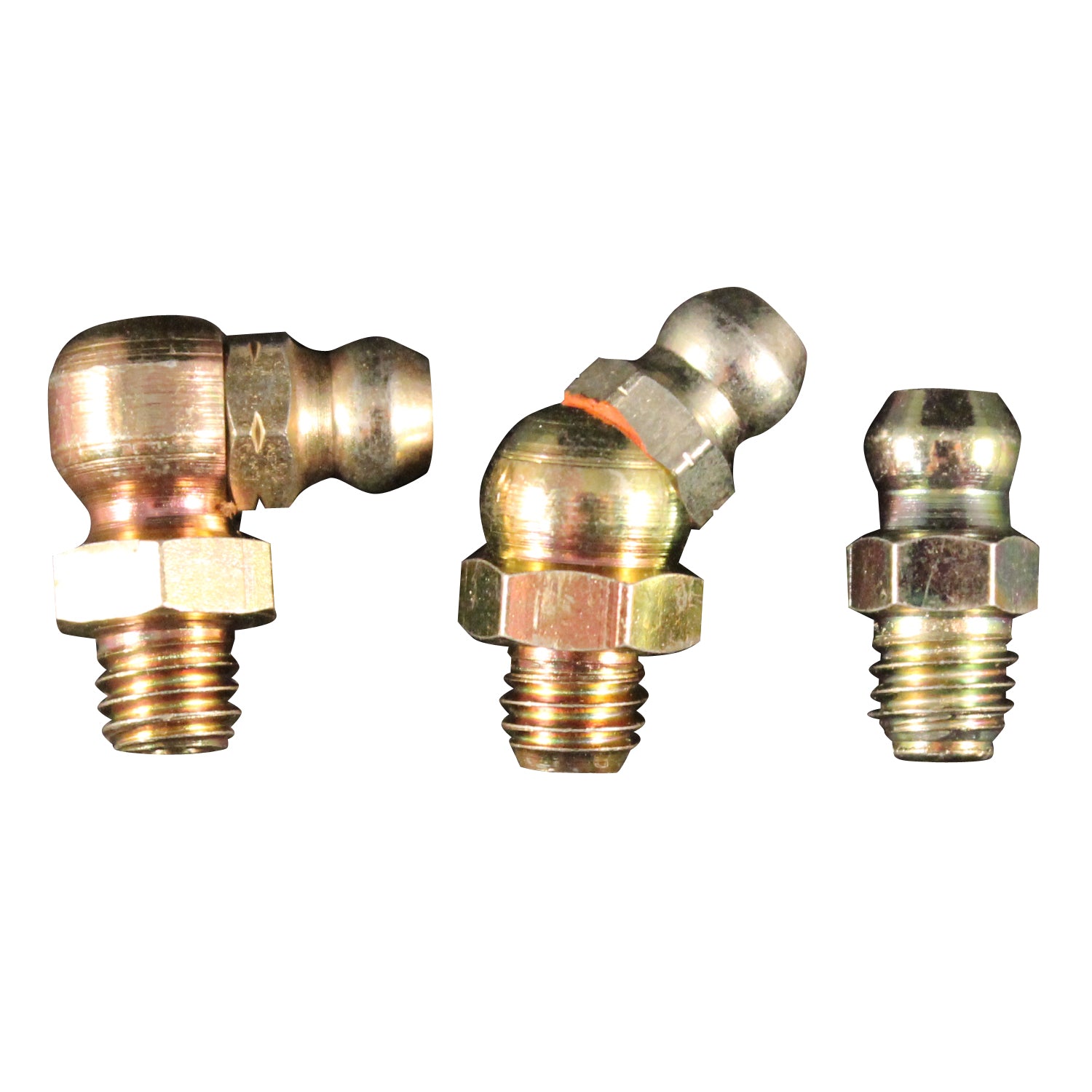
Grease fittings are small, threaded devices that allow grease to be injected into the bearings, joints, and other moving parts of machinery. They are typically made of metal, such as brass, steel, or zinc, and are designed to withstand high pressures. Grease fittings are an integral part of lubrication systems in a wide range of industries, including automotive, industrial, and marine.
There are several common types of grease fittings, each with its own unique characteristics and applications:
2.1 Straight (or Standard) Grease Fittings
These are the most common type of grease fittings, characterized by their simple, straight design. They are relatively inexpensive and easy to install.
2.2 Button Head Grease Fittings

These fittings have a button-like head that protrudes slightly above the surface. They are often used in applications where space is limited.
2.3 Flush Type Grease Fittings
These fittings are designed to sit flush with the surface of the component, minimizing the risk of damage or interference.
2.4 Elbow Grease Fittings
These fittings have a 90-degree bend, making them ideal for applications where access to the fitting is limited or awkward.
2.5 Crossover Grease Fittings
These fittings have two ports, allowing grease to be injected from either side. They are often used in applications where access to the fitting is difficult from one direction.
2.6 Pressure Relief Grease Fittings
These fittings are equipped with a pressure relief valve that prevents excessive pressure buildup within the component, reducing the risk of damage.
The primary function of grease fittings is to facilitate the delivery of grease to the moving parts of machinery. Grease provides several critical benefits, including:
Reducing friction: Grease acts as a lubricant, reducing friction between moving parts and minimizing wear and tear.
Grease fittings are used in a wide variety of applications, including:
Automotive: Wheel bearings, suspension joints, steering components, and CV joints.
Proper maintenance of grease fittings is essential to ensure the efficient and reliable operation of machinery. Regular maintenance includes:
Inspecting fittings: Regularly inspect fittings for signs of damage, such as cracks, leaks, or obstructions.
Proper greasing is critical for maintaining the performance and longevity of machinery. Undergreasing can lead to increased friction, premature wear, and even catastrophic failure. Overgreasing, on the other hand, can cause excessive pressure buildup, leading to seal damage and leakage.
Selecting the appropriate grease for a specific application is crucial. Factors to consider when choosing grease include:
Operating temperature: The grease must be able to withstand the operating temperature range of the equipment.
Grease guns are used to apply grease to fittings. There are several types of grease guns available, including:
Lever-action grease guns: These are manual grease guns that require the user to manually pump the lever to dispense grease.
If you are experiencing problems with grease fittings, such as difficulty greasing or leakage, there are several possible causes:
Clogged fitting: The fitting may be clogged with dirt or debris.
Grease fittings are essential components in many mechanical systems. By understanding the different types of grease fittings, their functions, and proper maintenance procedures, you can ensure the efficient and reliable operation of your machinery. Regular inspection, cleaning, and greasing of fittings will help to minimize wear and tear, extend the lifespan of your equipment, and reduce costly downtime.
I hope this comprehensive article provides you with valuable insights into the world of grease fittings!