Air Hose Connectors and Fittings: A Comprehensive Guide
Air hose connectors and fittings are essential components in pneumatic systems, facilitating the efficient transfer of compressed air to various pneumatic tools and equipment. These components play a crucial role in ensuring the safe and reliable operation of pneumatic systems across various industries, including manufacturing, construction, and automotive. This article provides a comprehensive overview of air hose connectors and fittings, covering their types, functions, and key considerations for selection and use.
Pneumatic systems utilize compressed air as their power source to drive various tools and machinery. Compressed air is delivered to these devices through a network of pipes, hoses, and fittings. Air hose connectors and fittings are vital components of this network, responsible for connecting and disconnecting air hoses, controlling air flow, and ensuring system integrity.

Air hose connectors come in a wide variety of types, each designed for specific applications and requirements. Some of the most common types include:
2.1. Straight Connectors
Straight connectors are the most basic type, used for simple connections between hoses and equipment.

2.2. Elbow Connectors
Elbow connectors provide a 90-degree bend, allowing for more flexible routing of air hoses.
2.3. Tee Connectors
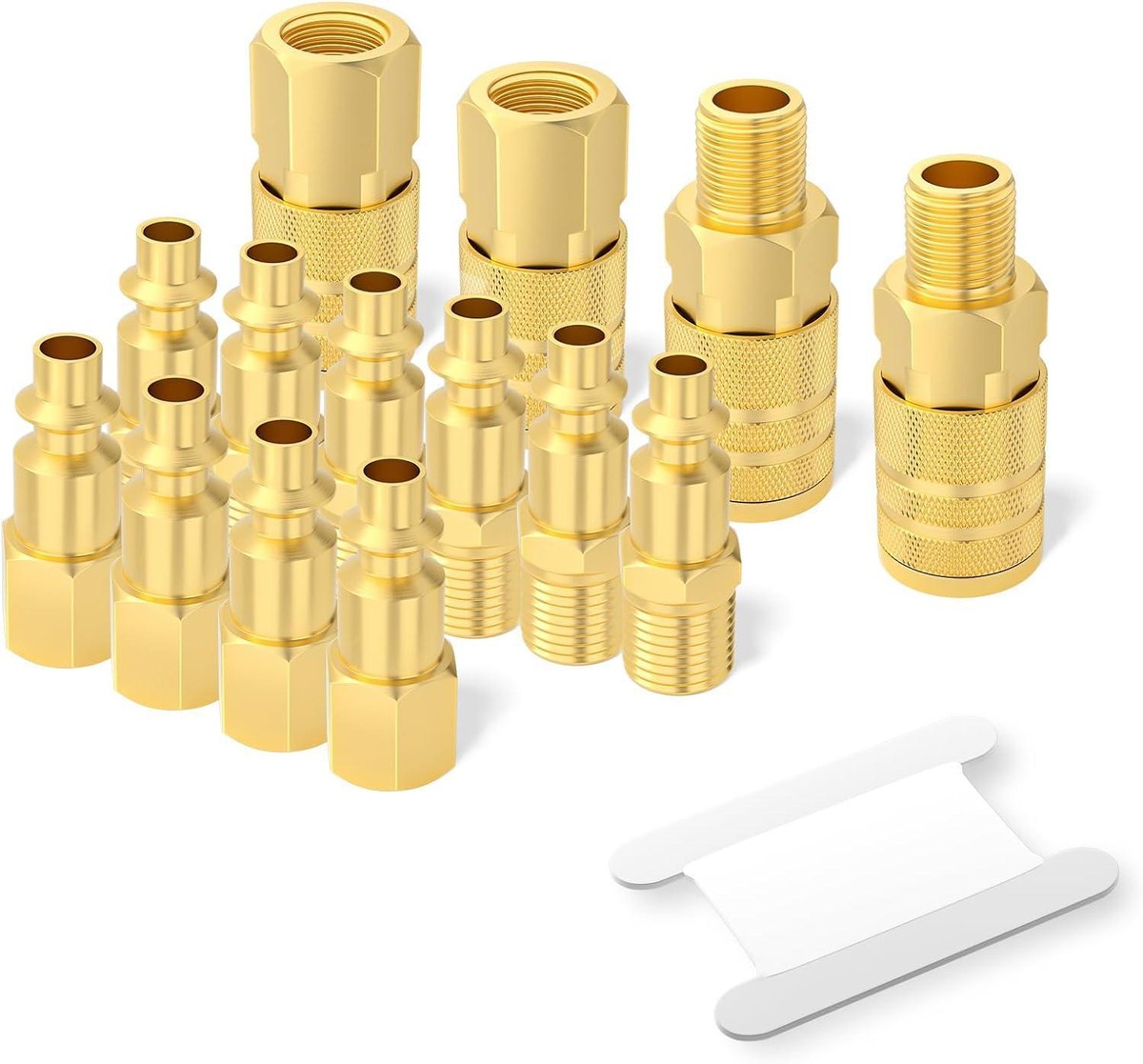
2.4. Cross Connectors
2.5. Quick-Connect Couplings
Quick-connect couplings are designed for rapid and easy connection and disconnection of air hoses.
2.6. Push-to-Connect Fittings
Push-to-connect fittings provide a simple and secure method for connecting air hoses to pneumatic components.
Air hose fittings are the components that connect air hoses to other parts of the pneumatic system, such as valves, cylinders, and other equipment. Some of the most common types of air hose fittings include:
3.1. Threaded Fittings
Threaded fittings are the most common type, featuring male or female threads that connect to corresponding threaded ports on equipment.
3.2. Flanged Fittings
Flanged fittings use flanges to connect to equipment, providing a more secure and robust connection compared to threaded fittings.
3.3. Grooved Fittings
Grooved fittings use a grooved coupling system to connect hoses to equipment.
Air hose connectors and fittings are typically manufactured from a variety of materials, each with its own unique properties and advantages. Some of the most common materials include:
4.1. Brass
Brass is a popular choice for its excellent corrosion resistance and good machinability.
4.2. Stainless Steel
4.3. Aluminum
4.4. Nylon
When selecting air hose connectors and fittings, several factors must be considered to ensure proper performance and system reliability:
5.1. Hose Size and Type
5.2. Working Pressure and Temperature
5.3. Application Requirements
5.4. Flow Rate Requirements
5.5. Compatibility
Proper installation and maintenance of air hose connectors and fittings are crucial for ensuring system reliability and safety.
6.1. Installation
Follow the manufacturer’s instructions carefully during installation to ensure proper connection and prevent leaks.
6.2. Maintenance
Regularly inspect connectors and fittings for signs of wear, tear, or damage.
Always use the correct tools and techniques when working with compressed air systems.
Air hose connectors and fittings are critical components of pneumatic systems, playing a vital role in ensuring the safe and efficient transfer of compressed air. By understanding the different types of connectors and fittings available, as well as the key considerations for selection and use, it is possible to design and maintain reliable and efficient pneumatic systems.
This article provides a general overview of air hose connectors and fittings. For specific applications and detailed information, it is essential to consult with qualified professionals and refer to manufacturer’s recommendations.