A Comprehensive Guide to Airline Fittings
Airline fittings are essential components in pneumatic systems, facilitating the connection and disconnection of air hoses and components. These fittings play a crucial role in various industries, including manufacturing, construction, and automotive. This article provides a comprehensive overview of airline fittings, covering their types, materials, applications, and considerations for selection and installation.
Airline fittings come in a wide variety, each designed for specific applications and requirements. Some of the most common types include:

Push-to-Connect: These fittings are easy to use, requiring only a push to connect and a pull to disconnect. They are widely used in various applications due to their convenience and speed.
NPT (National Pipe Thread): These are the most common type of threaded fittings, featuring tapered threads that create a seal as the fitting is tightened.

Swivel Fittings: These fittings allow for 360-degree rotation, preventing hose kinking and improving flexibility.
Airline fittings are typically made from various materials, each with its own advantages and limitations:
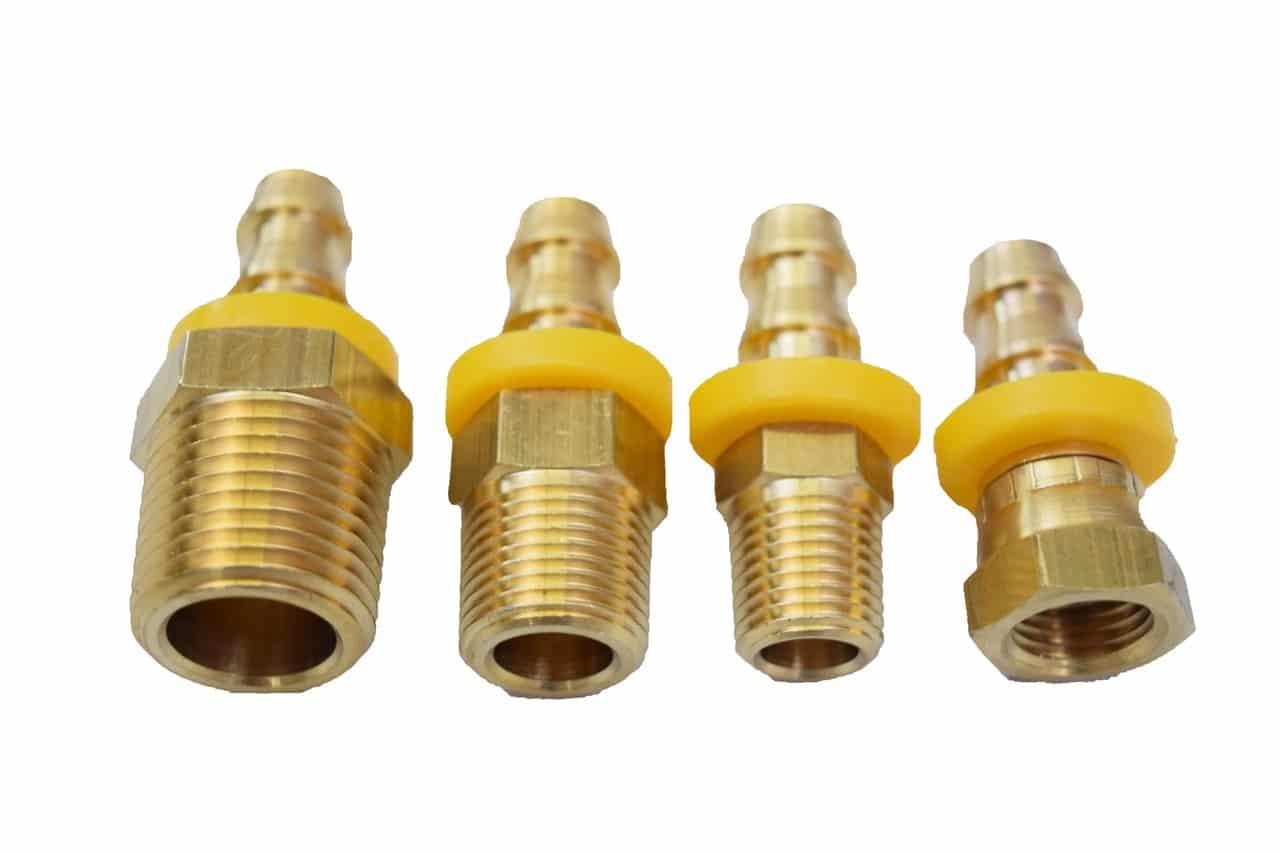
Advantages: Durable, corrosion-resistant, and readily available.
Advantages: High strength and durability, suitable for high-pressure applications.
Advantages: Excellent corrosion resistance, ideal for harsh environments.
Advantages: Lightweight and corrosion-resistant, suitable for low-pressure applications.
Airline fittings find applications in a wide range of industries and applications, including:
Pneumatic tools: Air wrenches, drills, sanders, and grinders.
Air compressors: Powering tools and equipment.
Tire inflation and repair: Air compressors and tire inflators.
When selecting airline fittings, several factors must be considered:
The pressure rating of the fitting must be higher than the maximum operating pressure of the system to ensure safe and reliable operation.
The flow rate of the fitting should be sufficient to meet the demands of the application.
The materials of the fitting and the hose must be compatible to prevent corrosion and ensure a long service life.
The fitting must be able to withstand the temperature extremes of the operating environment.
The fitting must be able to withstand vibration and shock loads without loosening or failing.
Proper installation of airline fittings is crucial for ensuring system integrity and preventing leaks. Some key considerations include:
The fittings and the surrounding area must be clean and free of debris to prevent contamination and ensure a proper seal.
Applying a small amount of thread sealant or lubricant can help to ensure a leak-free connection.
The fittings should be tightened to the manufacturer’s recommended torque specifications to prevent overtightening and damage.
The fittings should be aligned properly to prevent stress and ensure a secure connection.
Regular maintenance of airline fittings is essential for ensuring system reliability and preventing costly downtime. This includes:
Regularly inspect fittings for signs of wear, tear, or damage, such as cracks, leaks, or corrosion.
Periodically test the system for leaks using soapy water or other appropriate methods.
Replace any damaged or worn fittings promptly to prevent further problems.
When working with airline fittings, it is important to follow safety guidelines to prevent injuries and accidents:
Wear appropriate safety gear, such as safety glasses and gloves.
Airline fittings are essential components in pneumatic systems, playing a critical role in various industries. By understanding the different types, materials, and applications of airline fittings, and by following proper selection, installation, and maintenance procedures, it is possible to ensure the safe, reliable, and efficient operation of pneumatic systems.